Process
The intricate process behind developing the advanced multimaterial additive manufacturing system has so far involved the fusion of engineering expertise, innovative design, and rigorous prototyping. From conceptualisation to refinement, we’re revolutionising medical robotics and pushing the boundaries of additive manufacturing technology.
Technology
The integration of technology has empowered our robots to create complex medical components with precision, versatility, and efficiency, setting new standards in the world of healthcare innovation. Read below for more.
Outcome
Witness the transformative outcome of our pioneering project, as industrial robots equipped with advanced additive manufacturing systems redefine the landscape of healthcare, producing high-quality medical components with speed, accuracy, and customization.
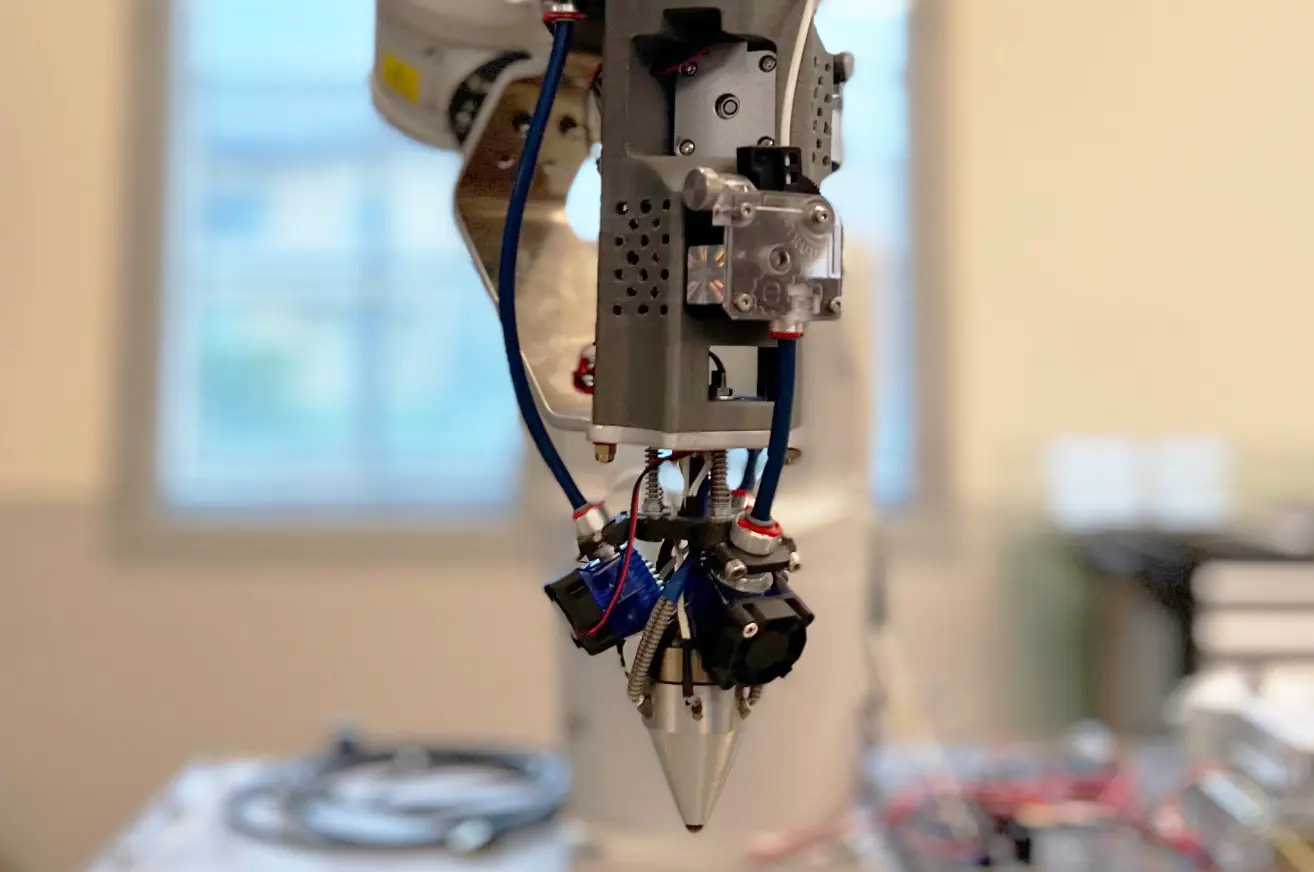
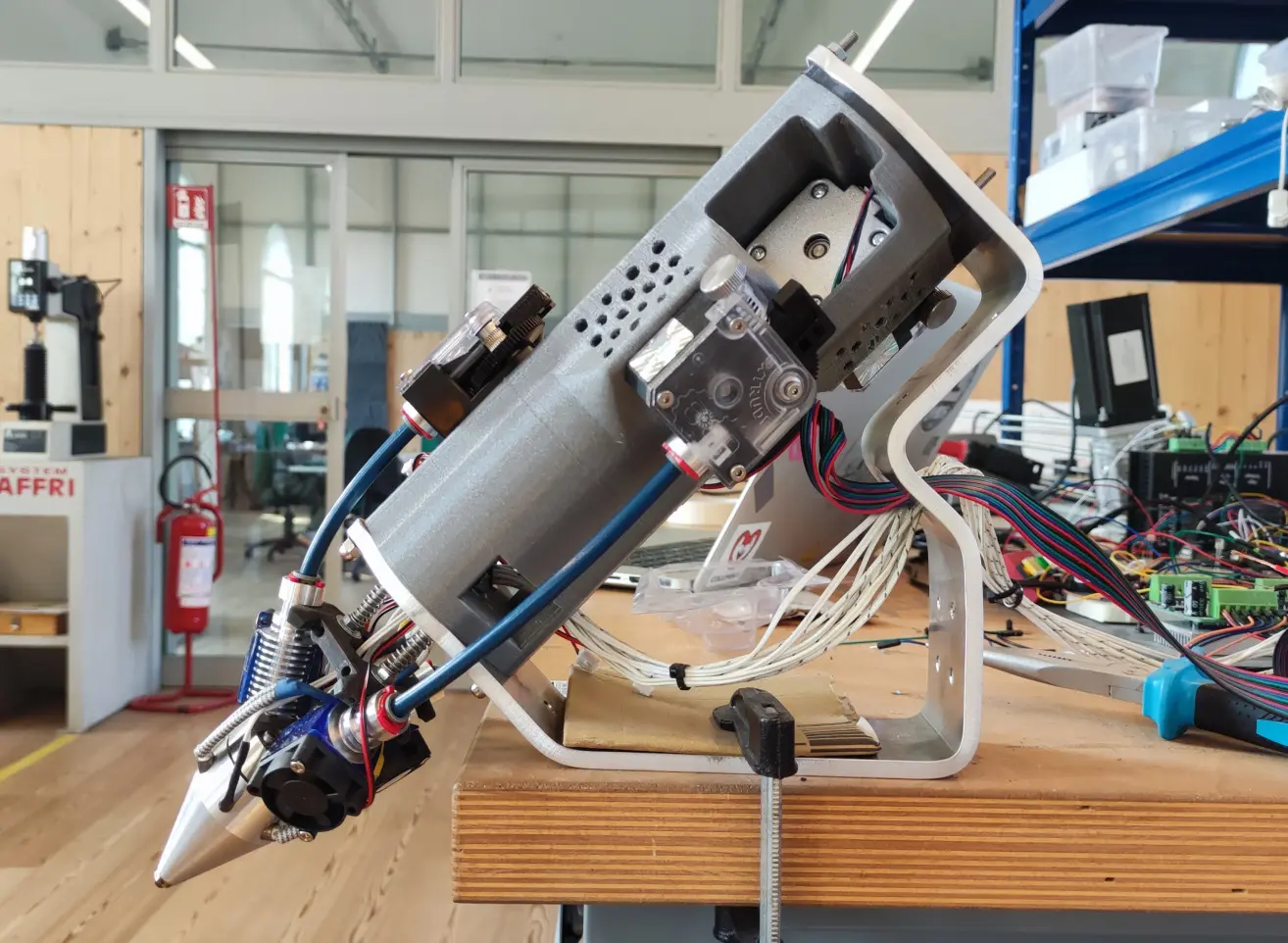
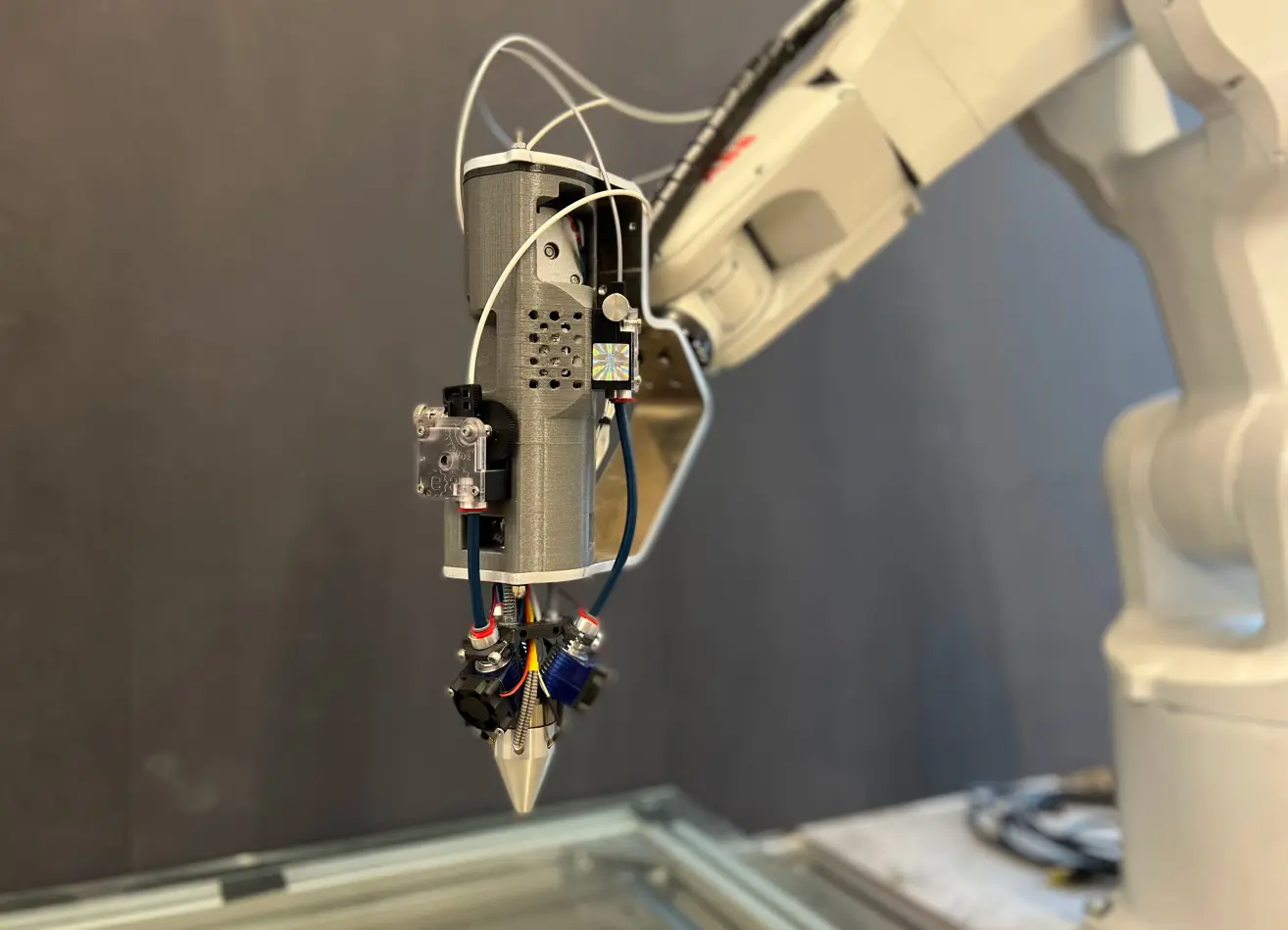
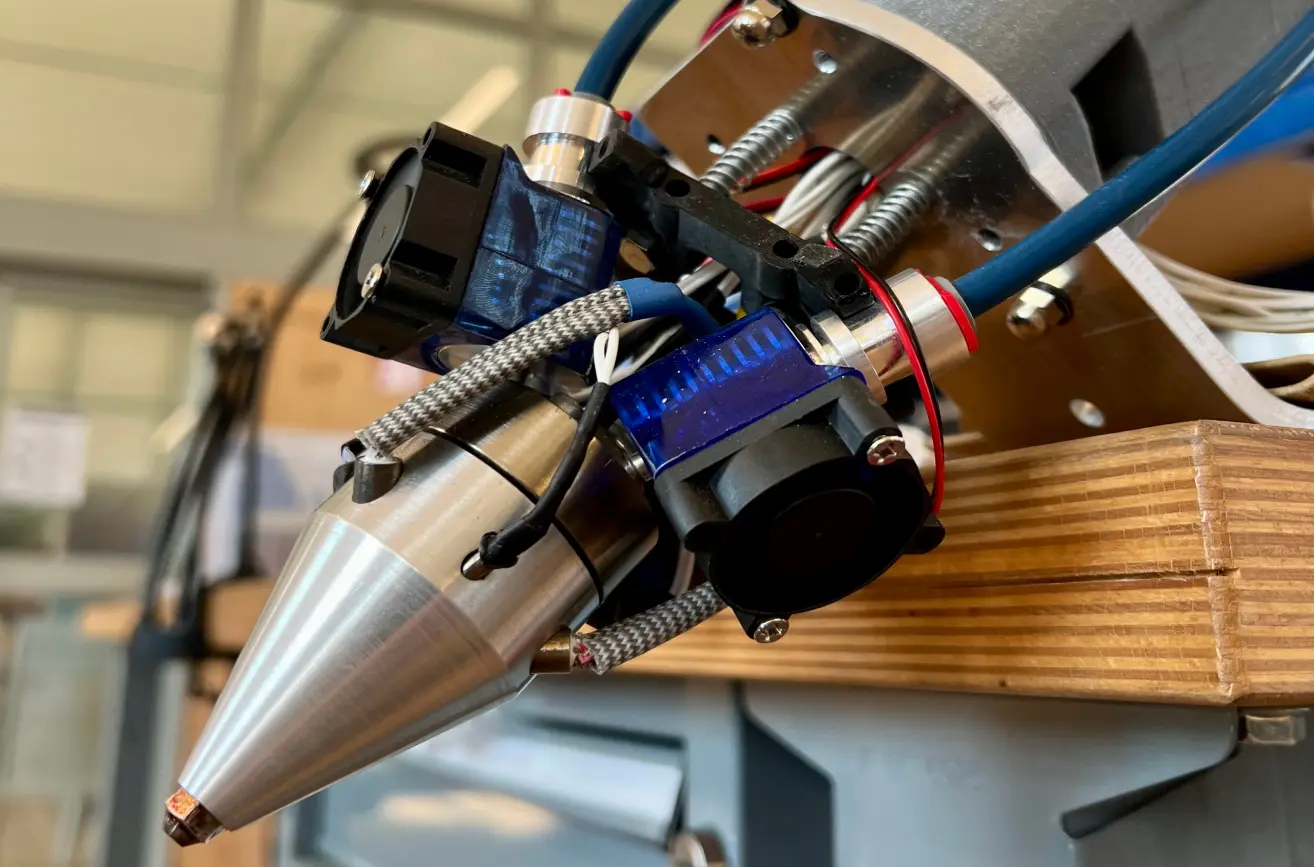